_small.jpg) |
Stocker drive shafts return for McAdoo
machine Company |
_small.jpg) |
Close-up of shafts showing detail of the work
performed |
_small.jpg) |
Another view of Stocker drive shafts
comparing old to new. |
_small.jpg) |
Close-up of gear teeth. |
_small.jpg) |
The stocker auger is mounted in Fixture to
facilitate welding. The welding buildup process was necessary due to extreme
wear of the auger flutes. |
_small.jpg) |
Close-up showing the work in progress during
the build up process. After Build up, the auger will be machined to the
proper specifications. |
_small.jpg) |
After cutting, to proper size, bar stock is
placed in the milling machine to begin millwork. The piece shown is the
beginning of a new bonnet for the injector assembly. The original part was
missing from the injector. |
_small.jpg) |
Close-up of bonnets milling process 1. |
_small.jpg) |
Close-up of bonnets milling process 3. |
_small.jpg) |
Close-up of bonnets milling process 3 |
_small.jpg) |
New bonnet mounted on injector assembly after
completion. |
_small.jpg) |
Rivets are removed to remove the tender
floor. If you review earlier web updates, you will note that the tender
floor must be replaced due to numerous large cracks and extensive wear. |
_small.jpg) |
Volunteer Charles Cantrell is shown removing
rivets with an acetylene touch. Care must be used not to cut the tender side
sheet. |
_small.jpg) |
The rearmost tender floor section is removed
after completing the rivet removal. The floor was removed in three sections
to maintain alignment of the tender side sheets |
_small.jpg) |
Interior view of tender showing rear floor
section removed. |
_small.jpg) |
Another view of tender interior showing
floor removed. |
_small.jpg) |
Volunteer Charles Cantrell maneuvers new
tender floor section into place while volunteer Walter Elvidge maneuvers the
crane. |
_small.jpg) |
Volunteer Walter Elvidge manipulates rear
floor section into place using a fork lift. At this point, the crane can no
longer be used. |
_small.jpg) |
The next section of flooring is readied to be
moved into position. |
_small.jpg) |
. Interior view of tender showing the first
two floor sections temporarily mounted into position. The sections are held
in place using nuts and bolts until they are finally riveted into place. |
_small.jpg) |
Exterior view of tender showing new
lower side sheets and tender floor. |
_small.jpg) |
Interior view of tender showing the complete
floor installed. Seems Will be welded prior to riveting. |
_small.jpg) |
Front view of tender showing new
stocker side sheets and new left side slope sheet being fitted. The old
right side slope sheet has yet to be removed. |
_small.jpg) |
Front view of tender showing continued
fitting of new stocker side sheets and new left and right slope sheets. At
this point, the old cistern front sheets have been removed and the new
sheets fabricated, drilled and replaced as well. |
_small.jpg) |
Another view of tender sheets being fitted. |
_small.jpg) |
Interior view showing stocker side
sheets and slope sheets being fitted. |
_small.jpg) |
Close-up of rear tender hold down plate after
removal of old rivets. |
_small.jpg) |
The scrap pile keeps growing. View of old
tender floor sections after removal. |
_small.jpg) |
Section of tender floor nearest the front of
the tender showing the extreme wear and rust. |
_small.jpg) |
Tender brake lever being milled after build
up work in the weld shop. |
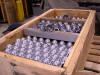 |
New stay bolt caps and sleeves arrive from
Northwestern Stay Bolt Co. |
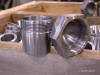 |
Close-up of cap and sleeve showing the
quality of workmanship. |
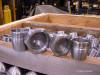 |
Another view of caps and sleeves. |
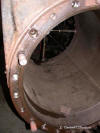 |
Close-up of front cylinder showing worn out
cylinder cover studs. |
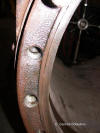 |
Close-up showing re-threading work on front
cylinders. The front cylinders required re-threading to accept new cylinders
cover studs due to the worn condition of the bolts and the wear on the
cylinder threads. |
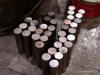 |
Bar stock is first cut to begin the
manufacture of new cylinder head studs. |
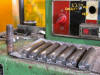 |
The bar stock is then faced and center
drilled. |
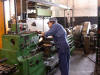 |
Volunteer Charles Cantrell at the lathe
facing and center drilling new studs. |
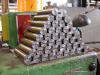 |
Close-up of finished work. Next the studs
will be threaded to the proper thread size. Each stud will then be hand
fitted to the cylinder and marked. |
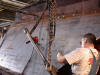 |
Volunteer Walter Elvidge checking new angle
of side slope sheet lip after bending. The slope sheets required re-bending
due to improper angle of the lip. Seen in the photo is the tool fabricated
by the contractor to do the bending. Assisting Walter in the bending process
were Charles Cantrell and the contractor. The re-bending of the two sheets
took two full days to complete. |
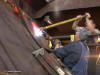 |
Due to the interference of the tenders curved
side sheet, a torch was required to heat the lip to facilitate bending. |
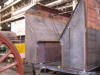 |
. View showing the front of the tender. The
sheets are nearly completed with all corners fitted properly. |